Brunner: Covid developments point way for future
There are two recent examples of new technology that are harbingers of where the graphics industry is heading in automation and leaner businesses, controlled and managed for optimum efficiency with minimised emissions and waste, writes print environmentalist Laurel Brunner.
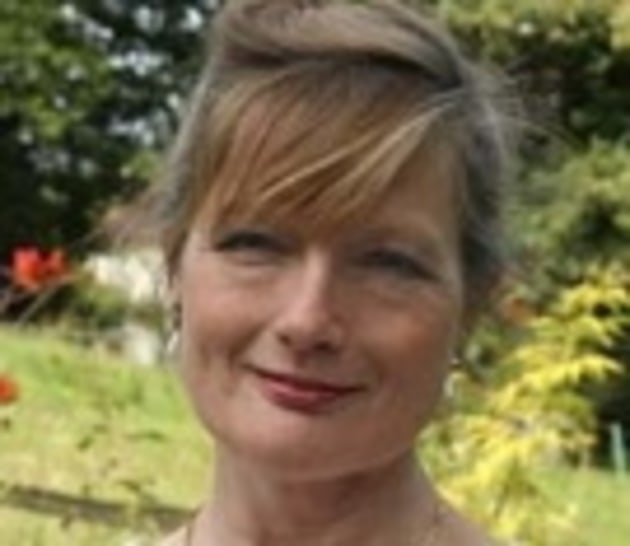
Global Graphics, for instance, is warming up to announce Harlequin 13, a timely nomenclature for 2020 but probably not unlucky for the company. Another manufacturer that comes to mind is Koenig & Bauer with its robotic plate changing technologies introduced as part of its pre-non-drupa sessions.
Whatever the calculations of governments and citizens around the world, whatever our wishful thinking and convincing denials, we will not be out of Covid for a long time. The coronavirus and its devastating effects on our economies, businesses, and lives are forcing people to rethink how their worlds function. For businesses, sustainability would appear to be taking a backseat to bigger problems of revenue generation and staffing levels.
The next bit of how businesses cope as Covid infections continue to spread, will be a rethink of costs and improved process control. Both of these can lead to more sustainable operations. Manufacturers in the graphics industry have developed the tools to make further automation possible, especially in distributed environments.
Global Graphics’ Harlequin technology is one of a handful of non-Adobe PostScript and PDF rip technologies to have survived the PostScript wars of the late 80s. It is the only clone rip able to outpace the Adobe technology, so it figures in many digital front ends (DFE) for high volume, high quality print output. The new version adds features for large format output, for instance for interior décor prints, textiles and corrugated packaging. To process massive TIFFs, JPEGs and PDFs the technology now features snazzy tiling tools, and the rip will also directly output PNG files, with enhanced sizing controls for all supported file formats.
Global Graphics is also improving support for larger digital front-end systems with for instance multiple rips on a single server for higher throughput volumes.
This is one of many examples of process automation that will improve the graphics industry’s environmental footprint. It’s especially helpful for very large format applications where mistakes can be expensive and wasteful.
The new Koenig & Bauer Rapida 106 eight-colour sheet fed press prints 20,000 sheets per hour with new feeder features for up to four different media types online, print units with easy to clean ink ducts and is “more or less maintenance free”. Using robots, it takes less than one minute for plate changes and up to ten plate changes can take place in the machine at once, during which time unit washing is done in readiness for the next job. Using robots to load plates into and out of the press means that there is no need to handle or bend plates, or risk them getting scratched. And it is quick.